Problem
Demurrage, storage,
operating changes, and
in-transit bunching — pipeline
management is an ongoing
challenge for rail shippers.
When there are too many cars
in the pipeline, demurrage/
storage charges are costly.
When there are not enough
cars, facilities risk running
out of inbound product, or
running out of capacity to store
outbound product. Or worse:
missing a sale.
ETAs and reports from the
railroads are helpful, but do not
provide a logistics manager
the full picture of their network
across all railroads. Assembling
the complete view manually
can be time consuming, and is
stale by the time it's shared with
other stakeholders.
Click image to view larger
|
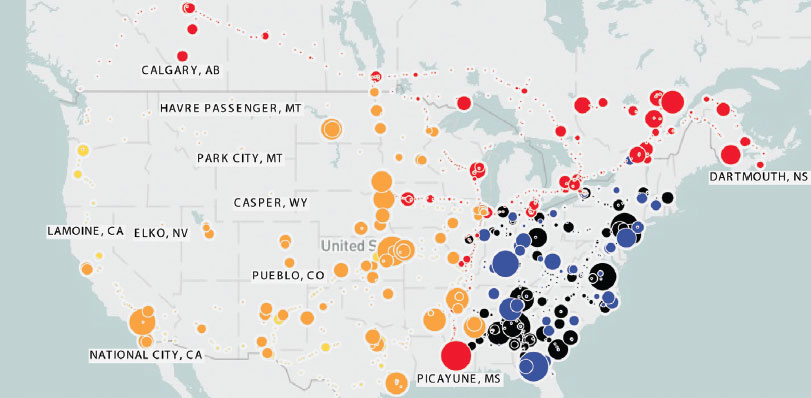 |
|
Step 1 — Configure an Accurate ETA
An accurate ETA is the basis of automating pipeline planning.
RSVP's ETA engine predicts arrival at destination yard for the full trip, not just to the next railroad. Driven by the current performance trend, recalculated for every event type, at every station, and recalculated when the car is stuck in transit, the ETA never gets "stale".
The ETA engine can be configured for each shipper's unique needs, such as day of week operating schedules.
Step 2 — Create an Automated, Real-Time Pipeline Report
The Pipeline Report comes as a fully built template in RSVP with a summary screen showing the number of cars in each status available locally, and the number of cars predicted to arrive on each day for the next 7 days, for every origin/destination in the network.
|
The template can be copied and customized for specific needs — for example, only specific STCCs, car types, sub-fleets, locations, or load/empty status.
Step 3 — Share the Information with All Stakeholders
Once the reports are customized and saved, they can be shared across all users, so that all stakeholders are making decisions off the same information. They can also be set up individually for each user.
The report is updated in real time whenever it is loaded by each user, which means the information never gets stale, and comments and hotlist flags added to railcars are visible to all stakeholders in real time.
The information can also be pushed by email. For example, stakeholders who are not system users, such as a transloader, could receive the report every day (or several times/day) via email.
Step 4 — Take Action!
With the latest, accurate information, organized in both a summary and railcar-level detailed format, available in the system or as an automated email report, the logistics team can start their day with the information needed to reduce operational inefficiencies.
For example:
- Identify which cars to order in next
- Plan whether or not weekend/overtime loading/offloading is needed
- Proactively identify the need for expediting by truck for bunching or in-transit delays
- Identify in-transit delays, such as bad orders, and the impact they have on ETA
- Analyze where receivers are not unloading and releasing railcars in a timely manner, and work with them to reduce the dwell time at destination in order to improve cycle times
For further information, contact sales@rsvprail.com.
ICL Systems
https://www.rsvprail.com/
|